This case study shows that, even if you seemingly do everything right, you can miss the forest for the trees.
The story takes place in a large complex manufacturing facility. This plant has three manufacturing lines, each line split into five sections. Everyone of the five sections has its own crew and supervisor. The nature of this plant is such that making these products is both an art and a science. This means the machine settings for the mould on this line would yield one result but, change just one thing, such as putting the same mould with the same settings on another line, and the results would change.
This, of course, impacted the manufacturing efficiencies, which had been steadily declining.
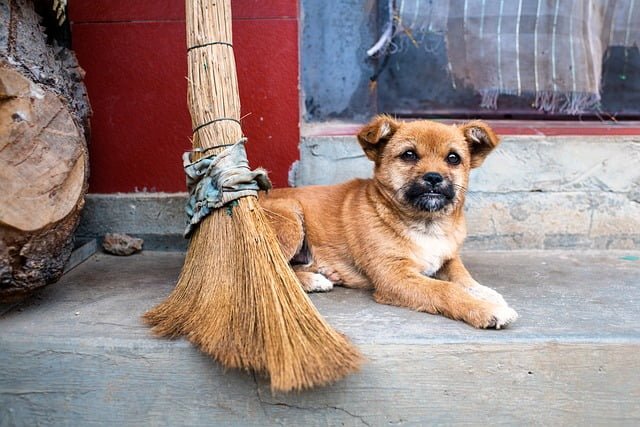
A new broom
The company had hired a new operations manager to tackle the declining efficiencies. And, as is the wont of a new manager, they wanted a clean sweep. So, all other projects were shelved and each section supervisor for each line was tasked with creating an improvement project. There were an additional four areas/ projects identified. This made for a total of 19 projects.
A structured approach
The Ops Manager had a very structured approach, which had worked well in his previous organisation. His approach was a nine-step process:
- State what the problem is
- Explain why this problem was chosen
- Ensure that the targets set are SMART
- Detail the manufacturing process in that section
- Show the data from before the improvement
- Do a root cause analysis for the causes of the problem
- Create an action plan to tackle the identified causes
- Measure the improvements, to ensure they are sustained
- Standardise the solution, to be rolled out in other areas
The Good
If you have read any of my previous articles/ blogs about poor project approaches, such as this one, this one, or even this one, you’ll know that the above is a great way to go. It makes sure a real problem is tackled and that the people affected by the project are on board.
The Ops Manager also made sure to halt other projects, to ensure the staff could focus on just this one project, in addition to their day-to-day responsibilities. This quick read shows the importance of doing this.
The goals of each project were SMART goals – here is an in-depth article about KPIs, making why this is important clear.
Each project had a project story board where the nine steps above were shown, and weekly stand-up meetings, ensuring that there was good communication within the project team, and to external stakeholders.
So, if there was so much good, what went wrong?
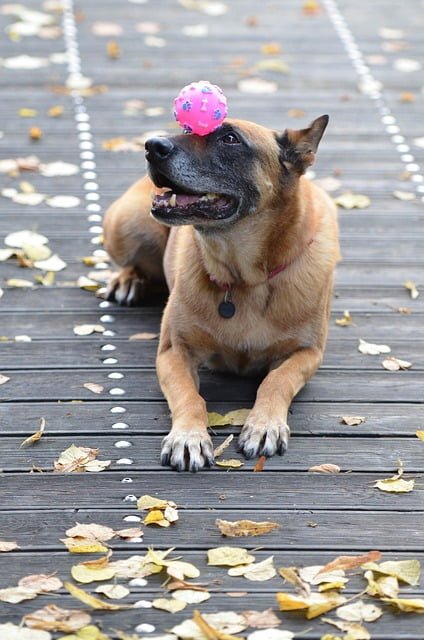
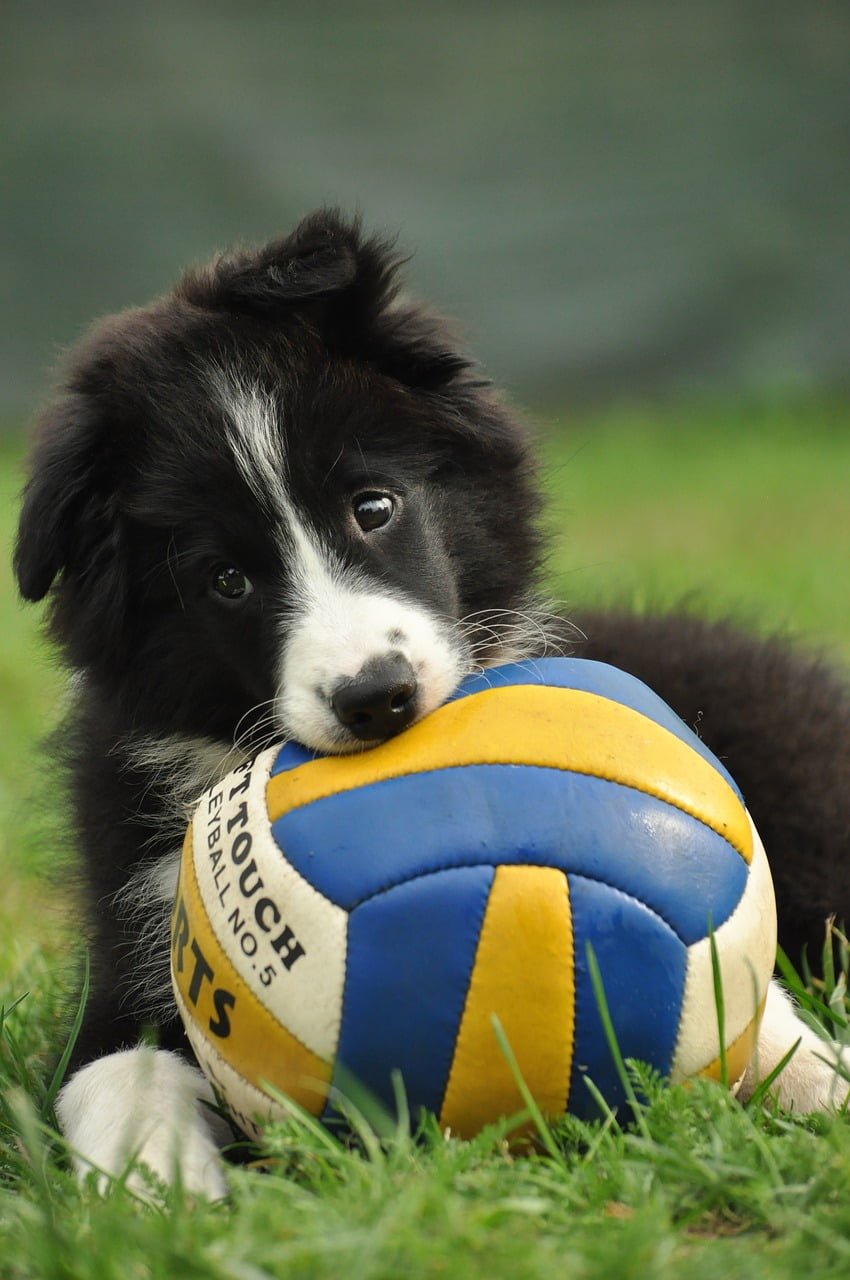
The bad and the ugly
The answer to what went wrong, and why the overall manufacturing efficiencies did not improve, is simple: the sum of the parts in this manufacturing system are greater than the whole. This simple answer does not make solving the issue easy though.
Essentially, working in isolation, each section was making improvements and focusing on their individual biggest issues. This silo mentality was not driving overall efficiencies in the end, as each change was being negated either by other changes on the line or because of a product change over.
Another contributor was the lack of resources. While each section was focused on their project, the supporting business functions, such as IT, HR, and maintenance, were shared across the entire plant, meaning teams where always waiting. This caused delays and had the support services rather frustrated.
What could we have done
A better approach would have been to place one project team for each manufacturing line and to focus on improving the total efficiency one product run at a time. This would mean that the line is worked on holistically, and the effect of these changes can be measured up- and downstream. Then, the learnings from each change can be applied across each line, and for each product.
The additional benefit would have been the reduced demand on the supporting functions, causing fewer delays.
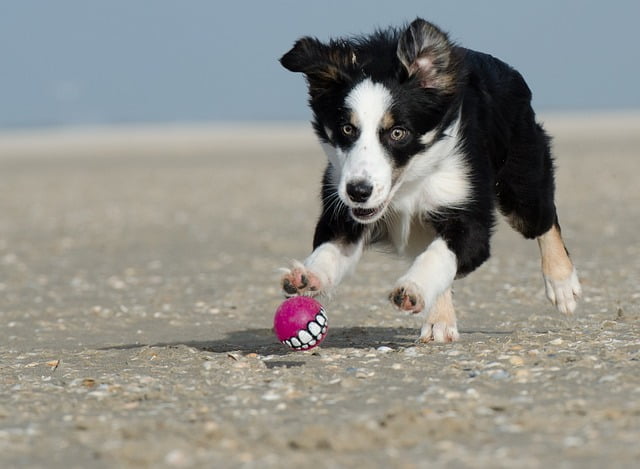