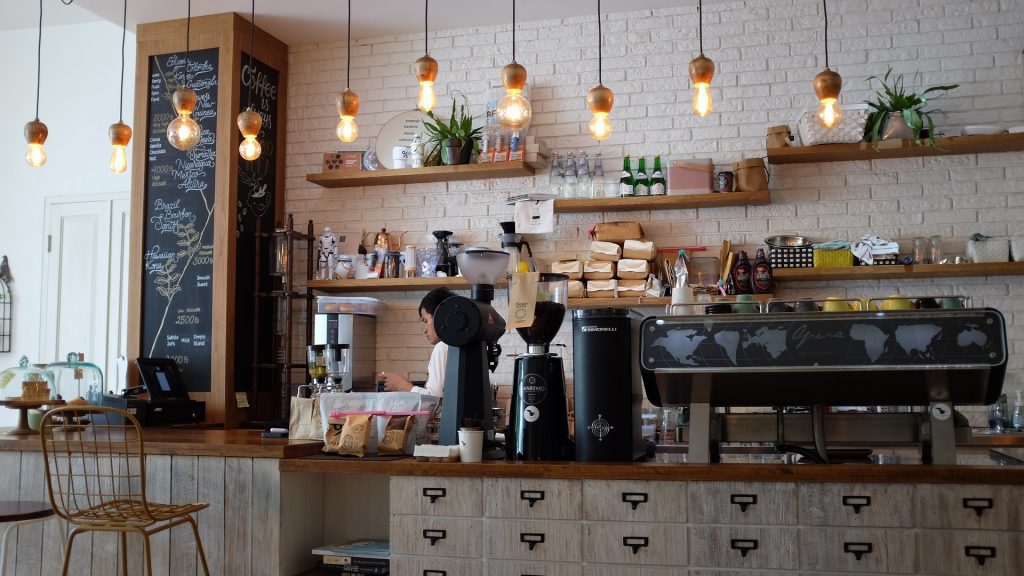
If you are anything like me, you enjoy a good cup of coffee. Quickly think about the steps to make coffee. Maybe you are thinking about making a cup of instant coffee, or getting a cup from your favourite barista? Let’s rather narrow it down, lets make coffee using a percolator as found in most offices.

Chances are your steps would have been something along the lines of:
1. Fill machine with water
2. Add new filter
3. Fill up with coffee grinds
4. Switch the machine on and wait for the coffee pot to fill up.
5. Pour coffee in a cup and add milk and sugar to taste.
The thing is that there are some very important steps missing. Likely these steps are missing, not because you forgot them, but because you do them automatically. Some of the typical unconscious steps most of us take include glancing into the water reservoir before filling it, to check the water level and ensure that the reservoir is clean. Similarly, you would have made sure that the coffee pot was empty and clean prior to placing it under the percolator. You would most likely also have checked that the pot was situated correctly to ensure that the coffee dripping out does not make a mess.
As you can see from the above, while making coffee is a relatively simple process, the required troubleshooting and small unconscious steps we take are integral to the process. Now imagine you have to show the new intern how to make coffee using the percolator, and they had never seen or used a percolator before. Each of the unconscious steps would be essential to be articulated.
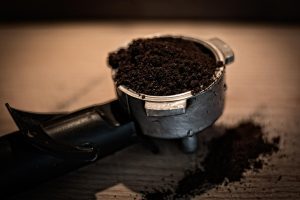
Why would we want to see the process flow?
As the example above shows, detailed process flows with trouble shooting are highly valuable for training. While the example of making coffee is a simple process, imagine the power of a detailed process flow for complex processes and procedures, where missing just one step could end in a disaster. Take for instance missing a credit check during the onboarding process for a new customer.
Clear processes which are used for training for both new and established employees ensure that the process is followed reliably that the results are predictable and consistent. Having a process flow that is clearly set out can make reviewing and improvement of the process much easier. It can then be used to show the before and after scenario, clearly illustrating how the improvement was made.
It can also be used to solve problems and troubleshoot issues. Take for instance the mystery of the coffee tasting different all of a sudden. Using the process flow, you would check that all the steps were followed. If that does not explain it, you could look at the materials used, such as the coffee, milk and sugar. From a troubleshooting perspective, if the percolator is leaking, you can start by checking if the pot was placed correctly or the coffee grounds have been overfilled, not allowing the water to drip through to the jug. Having a mapped-out process flows will assist in route cause analysis when something in the process goes wrong. A clear process flow can also identify shortcomings and highlight duplications or unnecessary steps.
The clearly envisioned and documented process can also be used to determine where checks need to be put in place, such as in-line quality checks. For instance, you could measure the temperature of the water and the colour and sweetness of the coffee, but this would not guarantee a nice cuppa. Instead, you would want to ensure you have the right amount of coffee grounds in the filter, wait until the entire pot has brewed and ensure that the required amount of milk and sugar are used.
Finally, having the process flow mapped out is a requirement for many international bodies such as the ISO certifications and is also one of the first steps to a successful process automation project. For instance, to automate the coffee making process, you know you would need a water reservoir, or a direct connection to water, you would need a place for the coffee grounds, or coffee beans and have a grinder, and a spout for the coffee to fill a pot or a single cup. The improvements that have been made while automating the coffee making process could include having a single cup being made at a time, from freshly ground coffee beans, all with just a single press of a button.

What constitutes a good process flow?
All the above benefits of a process flow can only be realised if it has been properly mapped and documented. A vague flow with unclear instructions and no clear start and end will hamper making process improvements. A good process flow should contain a verb and a noun, e.g. “Do something” or “Check Water Level”, in each block. Each block should be transformative, for instance in “Boil Water”, the water goes from room temperature to boiling.
A process flow should also show who performs each task, for instance for our automated coffee maker, the machine will grind the coffee beans, brew the coffee, but the person still needs to place a cup under the spout and press a button and then add sugar and milk.
Good process flows also indicate what is required for the process to be successful: in our example you need a percolator, coffee grinder, filters, cup and spoon and coffee beans, water, milk and sugar to make your cuppa.
Once you have a good process flow mapped, it can be optimised and then handed over. This could mean letting the intern make coffee or investing in a coffee machine. Image the power of having all the additional time and mental capacity to focus on your core business, by handing over or automating your none-core optimised processes.